About Potomac Yard
General Information:
Building Name- National Gateway Potomac Yard Land Bay E West
Location- Arlington, Virginia
Function- Office Building
Occupants- LA Fitness, Wachovia/ Wells Fargo Bank and others TBD
Size- 369,300 SF Base Building, Two Towers
235,000 SF Parking Garage Below Grade
Duration- 20 Months,1/2/2008 – 9/30/2009
Number of Stories- 9 plus a Penthouse
Cost- $75 Million
Project Delivery - Design-Bid-Build, GMP Contract
Project Team:
Contractor- James G. Davis Construction
Owner- The Meridian Group
Architect- Davis, Carter, Scott LTD.
Civil Engineer- Christopher Consultants
Structural Engineer- Smislova, Kehnemui & Assoc.
MEP Engineer- Allen & Shariff Corporation
Landscape Architect- Lewis Scully Gionet
Architecture:
The architectural design of the National Gateway Potomac Yard Land Bay E project contains many features that meet the requirements of LEED certification along with many A class materials used in the interior for its various tenants. The exterior of the two towers boasts a precast and glass façade with an intricate walkway that connect the two buildings. The building also accommodates the occupants with a spacious 235,00 SF underground parking garage that can house 600 vehicles. Another one of the key features of the building is a large indoor swimming pool that will be used by LA Fitness, one of the buildings occupants on the ground floor.
Major National Codes:
ICC/ANSI ADAAG A117.1-1998
ANSI A17.1 2000
VUSBC
IBC 2003
IMC
IPC 2003
CABO model energy Code
NFPA 2002
Zoning:
Parking garage plan change which involved 90 parking spaces changing into compact spots due to a curb projection of 6”.
Per Arlington County Standards a certain number of bike racks needed to be installed as per the ratio between the SQ footage of the building.
Arlington County Standards of a minimum of a 7’ driving clearance in the parking garage. This means to relocate and raise piping and conduit in the parking garage.
Building Enclosure:
The building façade of the Potomac Yard project consist of large precast panels that are placed between some large areas of glass panels. The glazing system that is used for the entrances and storefronts on this project is a typical aluminum rail and mullion system that is fabricated on site.
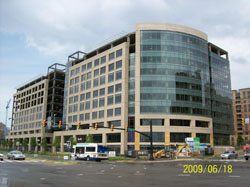
Roof:
The roofing system that is utilized on the Potomac Yard project is called a Cool Roof system. This is a type of roofing system is made of a single ply roofing membrane that is white in color so that it produces a high reflectivity of solar radiation. This roofing material is used to help reduce energy costs, maintain a comfortable building environment and reduce the urban heat island effect.
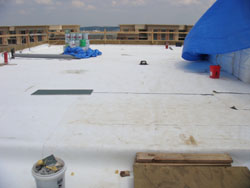
Sustainability Features:
This project is projecting a LEED Gold certification. One of the sustainable features of this project is the previously stated cool roof. Also on this project 40% of the building materials need to be regionally manufactured with in a 500-mile radius of the project location. All products that can be reused, returned, recycled, or salvaged must be documented and kept on record for LEED credits. On every typical floor of the building there will be recycling stations installed for easy access.
Construction:
The Potomac Yard Land Bay E is located next to US Route 1 and the George Washington Memorial Parkway in Arlington Virginia. Land Bay E is positioned near Reagan National Airport and south of Crystal City Virginia. The project is located on an old train yard that has been converted into commercial land development. Land Bay E sits on a 15-acre complex that is owned by The Meridian Group which houses a variety of buildings that range from hotel, office, residential and retail space. The large area of the site allows for two tower cranes, material hoists, deliveries, excavation and construction to take place with out disturbing the surrounding traffic flow and operations. Construction on the project began January 2, 2008 and it’s scheduled to be completed by September 30, 2009.
The project includes new construction of a three level underground parking garage which will house 600 parking spots and two building towers that reach 9 stories of office space. The project also includes the construction of an outdoor interim space that consists of a landscaped park with a one-story building structure that will house either a small restaurant or a retail store. This space will fill the void between Land Bay E buildings East and West.
Electrical:
The electrical service that is supplied to this building consists of a 3,000A 277/480V, 3 phase, 4 wire system that enters the building on the northern building elevation. The transformer vault for Land Bay E is located in the NW corner of Building A on Level P2. The main electrical room for the building complex is located in the NW corner of Building A on Level P1. There are 65 panel boards located throughout the parking garage and buildings A and B.
Lighting:
The lighting system that will be utilized for the typical floors on this project is most commonly 4’ fluorescent tube light fixtures that are operated on 277V. The reason for the common use of fixtures is because the interior of the building will be fit out at a later period when specific tenants are specified. Throughout the parking garage there are 16 different lighting fixtures that operate on both 120 and 277V. In the base building cores and finished spaces there are 36 different light fixtures being utilized on both 120 and 277V.
Mechanical:
The mechanical system that is utilized on this project is a Variable Air Volume (VAV) system that is supplied by (8) Air Handling Units (AHU), which range from 16,400-20,400 CFM on 480/3. There are (3) cooling towers and (2) 350-ton chillers that are installed on the roof of the building that are used to handle the cooling load for the building.
Structural:
The structural system that is utilized on the Land Bay E project is predominantly Cast In Place (CIP) concrete. The floor system is constructed of elevated post tension concrete slabs. There are a variety of concrete strengths that are used in this project. The slabs and beams utilize 5,000 psi concrete, slab on grade uses 4,500 psi concrete, walls and piers use 4,000 psi, pile caps use 5,000 psi and the CMU fill uses 2,500 psi strength concrete. The placement of the concrete for the project was performed by Miller and Long using a variety of placing tools which include: concrete pump truck, crane and bucket, direct shoot and Georgia buggies. All of the steel reinforcing being used on the project must meet ASTM A615, Grade 60.
The typical size of the concrete columns used on the Land Bay E project are 12’x12’ exterior and 16”x16” interior. The typical column bay size on a typical floor is 28’ wide with the use of an 8” slab and 72”x18” post-tension beams. The foundation that was used on this project is a deep foundation consisting of 14”x14” precast concrete piles with a bearing capacity of 125 tons. The piles were driven into the ground at an average depth of 30’ below the lowest floor level.
Fire Protection:
The fire resistance for the building ranges from 1.5 hours to 3 hours on certain building items. For the structural frame and bearing walls the fire resistance must have a minimum of a 3-hour rating, the floor construction must have a 2-hour rating and the roof must have a 1.5-hour fire rating. The fire protection systems utilized in the Land Bay E building consist of both wet and dry pipe sprinkler systems.
Transportation:
The Potomac Yard Land Bay E building project accommodates nine total elevators. For both buildings A and B four elevators serve each of the building’s typical floors and the three parking levels underneath of the two towers. The ninth elevator solely serves LA Fitness that only travels between floors P1 and Ground in Building B.
|